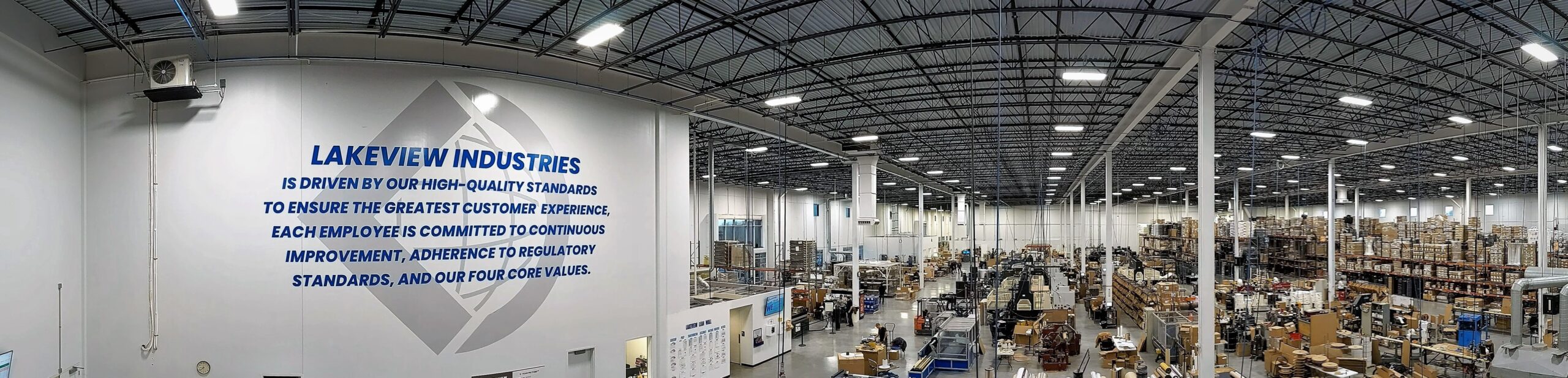
Lakeview Industries Streamlines RFQ to Production Workflow with Successful Paperless Parts Integration
The Challenge
Lakeview Industries struggled with estimating and quoting due to inefficiencies in their workflow, resulting in delayed RFQ response times and decreased overall productivity.
The Solution
Lakeview implemented Paperless Parts to streamline its quoting process, enhance collaboration, and achieve seamless integration with their ERP system.
The Results
-
Lakeview reduced its average requote turnaround time from 2 hours to 5 minutes and returns new quotes in under 48 hours.
-
Integrating into Lakeview’s ERP, quotes from Paperless Parts flow seamlessly and more accurately into production.
-
Ten cross-functional individuals involved in Lakeview’s quoting process can stay organized and connected within one centralized environment.
Background
With almost a half-century of experience designing and manufacturing flexible components for large OEMs, Lakeview Industries is a leading manufacturer in the Twin Cities area. They produce a wide variety of parts and converted engineered material solutions to fit a diverse range of business needs, delivering everything from gaskets to full-sized window sealing systems.
Lakeview serves as a true strategic partner to its clients and prides itself on adding value, offering competitive pricing, providing outstanding customer support, and developing innovative solutions. This comprehensive approach ensures that clients receive high-quality products, expertise, and solutions tailored to their specific needs.
Challenge
Lakeview aims to offer every advantage in the supply chain possible. “Our motto, plastered across our walls and embedded into our company culture, is ‘Good to Great,’” explains Ryan Chase, Controller at Lakeview.
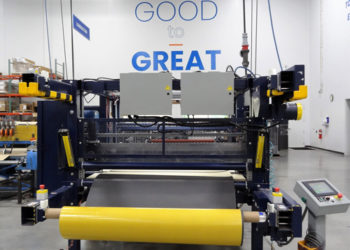
Last year, Ryan and the Lakeview team identified a critical business area needing significant improvement. “Our quoting process was slowing us down,” recalls Ryan. “We were quoting solely out of our ERP system—it was technically functional, but there were frequent, manual changes that needed to be made in order to support our quoting process.”
Holistically, Lakeview’s quoting workflow was inefficient: “Once we gathered all the relevant quoting data we needed, we’d spend a lot of time compiling each quote—building folders, hunting down documents, printing out papers—often needing to go back and forth for more information. We were building everything from the ground up each time.”
The inefficiency in Lakeview’s quoting workflow delayed their RFQ response times and burdened team members, affecting their overall productivity and ability to meet customer demands promptly.
Solution
The search for a more efficient quoting solution led Lakeview to Paperless Parts.
With Paperless Parts, Lakeview Industries has a comprehensive workflow system supporting engineers throughout the quoting process. Ryan explained, “When our engineers are building a quote, they know they’ll need all the material prices, and with Paperless Parts, we can easily determine the amount of material needed based on part placement. There are tools built into it that handle measurements we previously had to calculate manually in CAD software.”
Paperless Parts’ value extends beyond the engineering team: “We have a finance person like myself, three engineers, a VP of sales, and four account managers who all benefit from Paperless Parts in unique ways,” explains Ryan. “It’s definitely not just a quoting tool; it greatly enhances our collaboration.”
Various built-in tools help Lakeview stay organized, like automated quote setup, file management tools, and customizable dashboards. “Before Paperless, we’d have desks full of papers. Now, we have a sophisticated workflow that helps us manage every step of the quoting process in a single product.”
One of Ryan’s favorite benefits of Paperless Parts is being able to quickly re-quote work. “We have some customers that require a new quote every time they issue a PO and others that don’t order for nine months. With Paperless Parts, we can quickly go back to a quote from a year ago and update it with new technology or pricing. It eliminates a lot of redundant effort.”
That visibility also extends to the production floor; with the integration of Paperless Parts into their ERP system, Lakeview Industries has achieved a seamless workflow from quoting to production. “By integrating Paperless Parts with our ERP, once we win a job, our production process kicks off immediately.”
Results
With Paperless Parts, Lakeview has been able to see business impacts in the following areas:
- Time Savings: “We’ve seen a dramatic improvement in our speed for requoting jobs, going from 2 hours to 5 minutes,” Ryan shared. “We wanted to reduce our turnaround time to under 72 hours, but we are actually delivering most quotes in under 48 hours that are of higher quality and accuracy.” With more time on their hands, the Lakeview team has been able to quote more work, as well as divert seasoned team members’ energy into more strategic initiatives.
- Customer Communication: Paperless Parts helps Lakeview communicate more efficiently with production managers and engineers to get jobs onto the production floor faster. “We can often stay on the phone with the customer and update their quote in real-time. If there are material changes or labor cost adjustments, we can immediately pull up the old quote, make the necessary updates, and provide a new quote. You’re no longer going through that full start-over process, which can be really painful; it used to take four, five, sometimes six days of back-and-forth to get quotes finalized.”
- Visibility and Consistency: Paperless Parts has helped Lakeview Industries achieve better visibility and consistency in their quoting process. “With our centralized environment, novice engineers can now put quotes together and review them with experts, rather than needing assistance at every step,” Ryan explained. This helps drive efficiency and consistency across the team.
Want to learn how Paperless Parts can transform your quoting workflow?
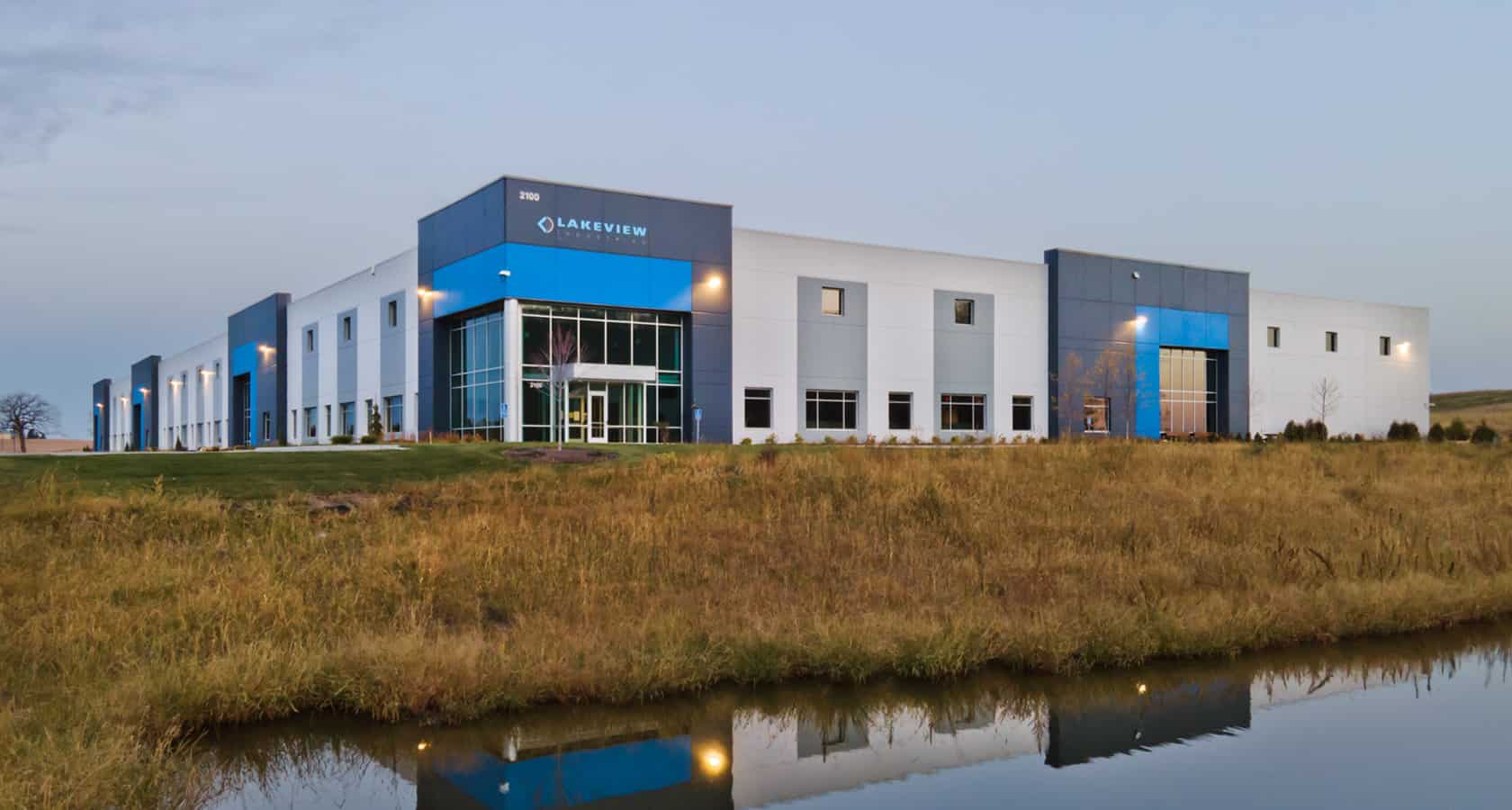
![]()
“We see Paperless Parts as the first step of production and a key part of the sales process. It’s been super helpful in eliminating silos across our team so we can all focus on the same goals.”